Metallic decorative film development story
金属风格装饰膜开发故事
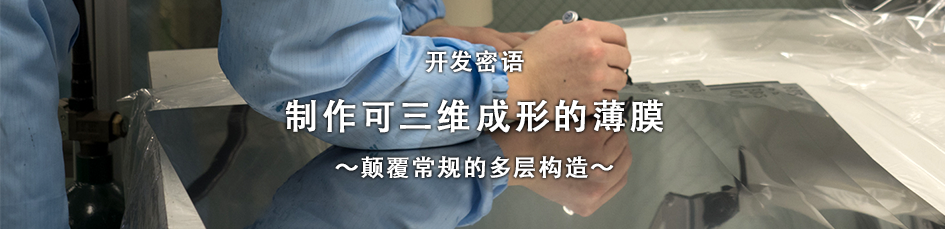
『来自美国的业务洽谈』
1998年,我们收到来自美国某企业的业务洽谈,该企业希望使用我们的金属风格装饰膜来制造三维成形的汽车后视镜外壳。
也就是不使用电镀而是使用膜片来装饰。当时,日本Wavelock株式会社(现 本公司)已有用于汽车车门夹条和保险杠装饰条的平面装饰用膜片,此次希望在三维零部件上也体现出同样的金属光泽。
当时,本公司产品阵容中已有用于汽车前后车窗框架的平面装饰用膜片,而该平面装饰用膜片也可以做到一定程度的弯曲。所以我们想到“结合该平面装饰用膜片与客户的加工方法,然后再设法改进的话会不会成功呢?”,就对部分加工用树脂重新做了改动,提交了试制品。
但是“三维效果虽然不错,与电镀相比却颜色发白没有金属感,而且硬度也不足”。
虽然实现了三维性能,却也产生了两个新问题。
『攻克金属感』
虽然膜片的状态不逊色于电镀,但是为什么制作成三维形状后会颜色发白呢?
为了找出原因并制定对策,我们从改良已布满灰尘的装置以再现变白现象开始,着手研究“什么样的金属才能在制作成三维形状的情况下也能维持其金属感。”
我们收集了各种各样的金属膜片材料,经过反复试验不断探索,终于在收到业务洽谈半年后得出了某种金属可以维持金属感的答案。
『表面硬度与成形性的矛盾』
如何提升表面硬度为好呢?
采用普通的表面硬化处理的话,三维形状成形后便会裂开。
于是寻找硬质材料并将其制作成三维形状成为了我们每日必做的功课。终于有一天,我们确认了某种材料的硬度和成形性,便试着将上述金属膜片包覆到了此材料上,但是又产生了另外的问题。
即成本昂贵。
在金属膜片贴合工序中,受此材料的厚度影响,加工费用上涨,这种状态下完全无法满足客户希望的价格。
『降低成本的挑战』
在金属膜片贴合工序中,薄且延展性好的材料是什么呢?
我们调查、咨询并收集了各种各样的材料,进行了反复验证。
某一天,我们偶然注意到用于制造饮料罐的可拉深加工的薄质材料。通过采用此材料,金属膜片贴合工序的加工单价取得了显著降低。但是,此材料表面硬度却不达标,因此,我们将之前发现的硬度和成形性优良的材料添加到了此材料的表层。
这样一来,“表面为硬质材料”、“金属层”这种多层构造的MITA(可三维成形的金属风格装饰膜)就诞生了。
『说服社长』
我们拿着用开发出来的膜片制作的三维样品向当时的社长汇报:“三维成形取得了成功,并且电镀感和表面硬度都能够保持”。
但是,当说明此膜片为多层构造时,却得到了“公司内有两道工序,此过程中会增加损耗和导致品质低下,不具备量产性”的回复。
即使这样我们也没有放弃,不断提交成本试算表、反复试制的结果报告,反复说明其在色彩变化的扩展等方面的优势,终于在重复这样的工作5个月后,取得了社长的批准。
至此,已经度过了2年的岁月。
『市场现实』
虽然金属风格装饰膜作为三维成形用商品得以上线,但是开始销售的前3年中,销量低迷。多是冰箱的触摸屏边框、汽车经销商自选零件等零星订单,公司内部的生产一直维持每月1次甚至停产状态。
『转机』
转机来自于一项“希望将汽车的车轮装饰从电镀改为装饰膜片”的议案。
当时该零部件由于电镀而产生了生锈问题,客户正在探索解决方法。因此对我们的三维成形用膜片发出了意向。由于是初次挑战汽车制造领域的产品,为了满足客户细微的外观要求、严格的规格标准,我们按照客户要求进行了前所未有的大量的试验,并准备了大量的资料。
功夫不负有心人,我们终于在1年后进入了量产阶段。
『摆脱电镀代用品的定位』
现在,我们在满足电镀、涂装都无法表现的富有底蕴的色彩构想这一客户需求的同时,还在不断的为了满足高品质需求而进行改善改良,致力于新产品的开发。
这是因为我们一直有一种如果被定位为电镀和涂装代用品,不具备功能性的话,最终将会被卷入单纯的价格竞争的危机感。
近年来,汽车和家电等工业用品都会安装各种传感器,因此对不阻碍特定波长的电磁波的装饰材料的需求日益高涨,我们现在也正致力于此类产品的开发。
以“世界第一的品质和系列产品让客户感到高兴”为目标。

『旅行用行李箱项目的经验』
~获得了能够实现色彩多样化的技术~
从2000年当时,在国内市场评价通过使用金属风格装饰膜的话,可以使用轻量的塑料来表现高品位的铝包。在2007年作为旅行用行李箱的表皮材料,不少的日本国内客户和我司洽谈带有金属感的金属风格设计企划。因为比公文包更大,需要考虑飞机上的装载重量,所以本来是很难采用金属材料的领域。但是如果能够使用金属风格装饰膜的话,可以解决重量限制的同时,还可以实现金属设计的差别化。但是在企划阶段,已经决定了该形状的行李箱有6种颜色,在开始搭配的同时,进入了金属风格+色彩表现的Try&Error(尝试错误)。除了加工方法和着色材料的设计之外,还需要解决以作为行李箱的耐冲击性在内的产品检查项目。经过约1年的开发期间构筑了全色产品的生产体制。同时,获得了金属风格的调色控制技术,为以后的汽车零件的展开获得了强力的武器。
『通过透光零件获得的成长』
~加强质量管理~
随着汽油车向电动车(EV)的过渡,搭载LED背光灯的车辆零部件的企划呈增加趋势。在背面设定透明的树脂,从背面点亮LED,白天表现金属外观,夜间表现发光效果的零件。由于背面的基材为无色透明,至今为止也对应了小型的透光零件,2016年左右,象征汽车制造商的车辆外饰的车标也开始以具有透光性能的概念设计。这些零件也被称为汽车的脸面,需要特别严格的表面质量管理。曾被指出缺少有微细的金属层脱落现象,工厂相关人员全体出动调查了原因,结果发现在特定的导向辊接触时存在微小的摩擦。验证了最适合于基材输送的辊表面,并采取了相应的对策,能够明显地改善被指出的细小金属层的脱落不良。在与该效果相关的对象设备上也横向展开,可以使得对策效果更加坚如磐石。
『应对不断变化的透光效果的需求』
~透光色的控制~
在透光零件开始被广泛认知的某一时刻,就接到了来自客户的透光色的调色要求。通过金属层使LED光源发光时,希望解决色相从光源主体的显色偏离的问题。与此相对,需要制定控制透光色的方法。
在全部掌握了每个基材的透光色之后,根据偏移的色相在膜片背面配置与偏移相对的颜色成分,从而成功控制透光色。由于是金属层背面的改良,所以能够不改变LED熄灭时的金属外观设计地进行透光色的管理,能够满足要求。
『对欧洲市场的提案和新的课题』
~透毫米波性能的表现~
到了2019年,欧洲的子公司开始有客户询问被称为毫米波的频带的透电磁波性能。“想把探测车距的雷达传感器配置在前车标零件的背面。以往的电镀制会屏蔽毫米波,所以能否有效利用膜片?”之类的咨询。在金属风格装饰膜中,根据金属层的状态,可以表现透毫米波的性能,但在设想了对膜进行热加工后的工序上,认为实施金属层的管理还存在课题。因此,详细验证了金属原子的状态和各层厚的透电波性能, 进行了能够稳定再现透毫米波性能的金属层状态的把握和对制造工序的反映。进而,确立膜片形状下的性能验证方法,能够提供表现透毫米波性能的金属风格装饰膜
截至2023年,世界各地都在急速变化,汽车产业周围的环境也在持续着瞬息万变的变化。CASE(连接·自动驾驶·共享·电动化)的普及,MaaS(移动手段服务的提供)商务模型,从ICE(内燃机)到EV和燃料电池车(FCV)的变迁,以温室效应气体(GHG)削减为主的ESG(环境·社会·企业统治)意识的提高。在这样的背景下,全世界的相关人员都在寻找最合适的姿态,在这种情况下,我们如何将WAT所拥有的优点融入潮流呢。与之前相比,更需要带着速度感和柔软性,以及作为队伍的一体感前进。